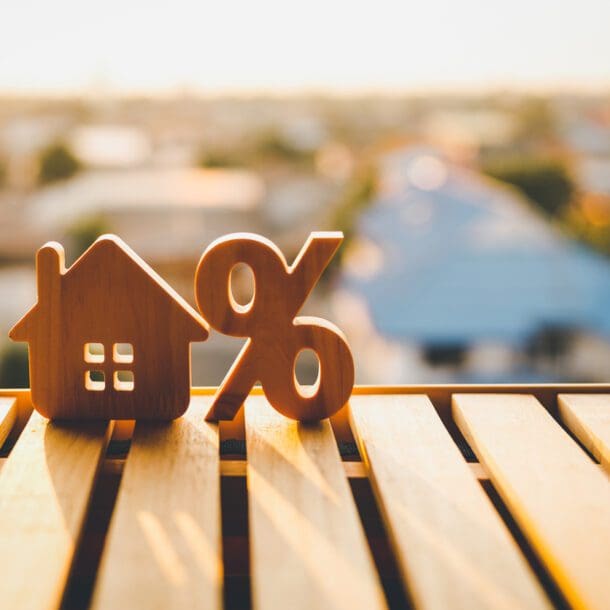
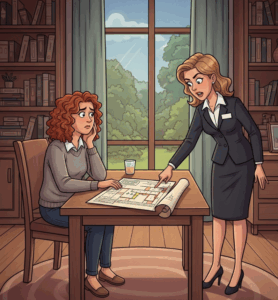
Folks outside the building and design professions sometimes use the terms high-performance, green, sustainable, healthy, energy-efficient, net zero and resilient interchangeably. But they are not the same.
“High-performance” is actually an umbrella term for the many approaches to making better buildings. Each approach focuses on one or more of the goals listed above. Each one uses specific design strategies. And each one defines high-performance in its own way.
For example:
The various methods may be used in more than one high-performance approach.
Since the dawn of human history, we humans have created structures of various kinds to protect ourselves from the elements and predators. Comfort was of secondary importance: nice to have but seldom achieved.
The nineteenth century German architect Gottfried Semper called such buildings “Primitive Huts.”
Over the millennia, modest improvements in building technology made shelter increasingly accessible. A small minority of buildings provided a modicum of comfort. But the standard remained quite low.
Cheap, plentiful fuel made it easy to maintain the status quo. Cold, drafty building? No problem! Just throw some more wood or coal in the stove! Over time, oil and natural gas became popular heating fuel options.
A popular notion—that buildings need to breathe—meant that fresh air entered and left living spaces through leaky walls. The only catch is, the “fresh” air picked up contaminants along the way, such as mold, dust and rodent feces. Not so fresh!
Until the mid-to-late 20th century, there was little impetus to change. People didn’t know about the negative effects of standard building practices on the environment and human health. And our buildings reflected that. Most buildings—new and old—were still woefully inefficient, uncomfortable, and unhealthy.
An oil crisis in the early 1970s caused us to think about improving building performance, temporarily, but interest waned when oil prices stabilized. Climate change has had a more shocking and enduring effect on us.
Now we understand that carbon dioxide and other greenhouse gases, which come from burning fossil fuels, are an existential threat. And we also know that buildings are a big part of the problem: In the U.S., buildings consume 70% of the electricity produced and generate 39% of the carbon dioxide emissions.
Both public and private sector entities have responded with a dramatic uptick in building science research and policy changes. Building and energy codes, for example, have improved building performance in many (but not all) states. Improvements have focused on thermal insulation, however, while indoor air quality and airtightness have received less attention. It is worth noting that code requirements represent minimum standards, not best practices.
In the next section, I explain 6 ways to achieve high performance in buildings.
A building envelope or enclosure physically separates the exterior environment from the interior environment. That includes the roof, doors, windows, floors and walls. A well-insulated building envelope slows the flow of heat into and out of living spaces. A poorly insulated building will be uncomfortable for occupants and expensive to heat and cool. HVAC equipment will have to be oversized—and therefore more expensive. And it will have a shorter lifespan because it cycles on and off frequently.
There are many types of insulation. Where moisture is not a concern, air- and vapor-permeable types may be appropriate. These include mineral wool, fiberglass and cellulose. Where there is condensation or a flood risk, foam plastic insulation types are a better choice. These include EPS, XPS and Polyisocyanurate board and polyurethane spray foam.
Using the right kind of insulation is critical. For example, using fiberglass to insulate the walls in a basement that is prone to flooding is simply a bad idea. Likewise, installing it in your roof may cause the sheathing to rot and/or grow mold.
How we install insulation also matters. Continuous exterior insulation is more effective than cavity insulation (i.e. between framing members). In a typical wood-frame building, 27% of the building envelope is framing. Framing lumber is a mediocre insulator. Wall studs and roof rafters serve as “thermal bridges,” pathways for heat gain and loss. Continuous insulation interrupts those pathways and saves energy. A bonus: it also helps to protect the structure from the elements.
It’s also important to have the right balance of insulation between the different parts of the envelope. Even the best insulated windows will not resist the flow of heat as well as a poorly insulated wall. What’s the point of super-insulating your walls and roof if you’re going to use poorly insulated windows and doors?
Perhaps the most important benefit of thermal insulation is that it reduces the use of fossil fuels. Burning fossil fuels creates greenhouse gases, which contribute to climate change. So, a well-insulated building can save money and help the environment: a win-win.
But there’s more to it than that. Certain plastic foam insulations, such as XPS and spray foam, are blowing agents that exacerbate climate change. In other words, by using certain insulation products to combat climate change, you inadvertently might be making it worse! Or, at least, not helping as much as you might expect.
If this sounds complicated, that’s because it is! The various assemblies and parts of a high-performance building are part of a system and must be compatible. It’s also important to consider the climate implications of our insulation choices. If you are unsure about the best way to insulate, we recommend that you consult an architect who specializes in building science.
High-performance buildings control the unwanted inward and outward leakage of outdoor air through cracks and gaps. Building science experts generally agree that airtightness is as important as thermal insulation.
Old buildings are known for being leaky and drafty. While they have the benefit of being able to dry out when they get wet, which prolongs their lives, the “fresh” air they bring in to occupants likely includes contaminants such as dust, rodent feces and mold.
When you turn on a bathroom exhaust fan or range hood in a leaky building, the negative pressure you create draws in those contaminants. It also draws exterior water and water vapor into the walls. That trapped water can lead to rot and mold.
Leaky buildings also require a great deal of energy to heat and cool. Ironically, the oversized HVAC system you’d need in a leaky building will create positive pressure, which forces the conditioned air through the cracks to the exterior. More expensive equipment, running more often, using more energy. It makes no sense!
High-performance buildings achieve airtightness with peel-and-stick membranes; adhesive tapes; sheathing impregnated with an air barrier film; or a combination of these items. With sufficient thickness, closed-cell spray foam can also act as an air barrier.
Another benefit of airtightness is that it protects the structure from the elements. That increases the building’s durability.
A high-performance building technician can perform a blower door test, which will measure airtightness and help locate leaks. It’s a good idea to seal all leaks before installing interior and exterior finishes.
People need fresh air. In low-performance buildings, people get air through leaks and gaps. But, as noted above, that air is far from fresh.
High-performance buildings are nearly airtight, so bringing in fresh air and removing stale air must be intentional. It is possible (and wise) to do that in a way that conserves energy.
Energy-recovery ventilators (ERVs) and heat-recovery ventilators (HRVs) do just that. These balanced ventilation systems intelligently combine exhaust- and supply-air ventilation to maintain air pressure without drastically increasing overall energy consumption. That energy consumption includes both electricity to run the HRV or ERV and the energy required to condition the supply air.
HRVs and ERVs are similar in that they have a core through which incoming and outgoing air travel. Both HRVs and ERVs transfer heat. But only ERVs transfer moisture as well. In many climates, there is not a definitive answer to the question of which is the right choice. However, there are a few guidelines to consider.
Buildings in the hot, humid areas, such as the South and East, will usually use an ERV. An ERV can retain humidity in winter in cold climates and reject humidity in warm climates.
Buildings in dry areas, such as the West, typically use HRVs. HRVs have a lightly higher heat recovery efficiency.
Connecting an HRV to a ground loop of glycol with a small circulating pump can do a lot to boost its efficiency. The temperature of the soil several feet below the surface is warmer than the air in winter and cooler than the air in summer. The soil temperature is transferred to the glycol, which pre-heats or pre-cools the fresh air entering an HRV.
Aside from fire, moisture is the greatest enemy of buildings. Rainscreens are essential for buildings because they help keep moisture out of walls. And they prevent the moisture that does get in from being trapped and doing damage.
Because of their ability to manage moisture, rainscreens are especially beneficial in climates prone to heavy rain, wind-driven rain, flooding, or high humidity. They are a common feature of high-quality projects, both new construction and retrofits. Yet (incredibly) the building code does not require them.
Key components of a rainscreen system include:
Cladding: This outermost layer of a rainscreen assembly can be thought of as the rain control layer. It can be made of various materials, such as metal panels, fiber cement, brick, stone, or even wood clapboards. The cladding is a “screen” that protects the building from the direct exposure to rain, wind and snow. While the cladding keeps out the bulk of the water, it is not a barrier. Over time, cracks and gaps can form as cladding material shrinks or caulk fails. That is why cladding is only the first of a few layers of protection.
Drainage Gap: Behind the cladding is an airspace that can be up to one inch thick. This space allows any water that penetrates the cladding to drain out the bottom of cavity. A better variation of the drainage gap is the Drainage and Ventilation Gap, which incorporates vents at both the top and bottom of the wall assembly. These vents promote the upward movement of air, helping to evacuate moisture and maintain a dry environment behind the cladding.
Water-Resistive Barrier (WRB): The next line of defense in a rainscreen system is a water-repellent membrane that prevents water from entering the building envelope. Building paper, house wrap, sheet- or trowel-applied membranes, foam insulation and coated structural sheathing are all examples of WRBs. For a WRB to be effective, it must be continuous and integrated with flashings to other enclosure assemblies, such as roofs, foundations, and windows. Lapping the WRB components (think shingles) and taping or sealing the joints of the material ensure the necessary continuity.
Rainscreen systems offer many benefits:
By creating a barrier against direct water ingress and providing a pathway for drainage and ventilation, rainscreens help prevent moisture buildup within the building envelope. This reduces the risk of water damage, mold growth, and structural deterioration.
By managing moisture effectively, rainscreens extend the life of building materials and reduce maintenance costs. Imagine, for example, that wall cladding becomes wet during a rainstorm on a hot summer day. When the sun returns, the cladding heats up and the water it contains begins to evaporate from all sides. If the cladding is installed as part of a rainscreen, the moisture can easily exit the wall through holes at the top of the drainage gap. If the assembly lacks an airspace, the sun will “drive” the moisture deeper into the wall, where it may become trapped and ultimately cause the wall to rot.
Rainscreen designs can also improve the thermal efficiency of a building by reducing heat transfer through the exterior walls. In a low-performance wall, the heat on a hot summer day will make its way to the interior spaces, and the air conditioning system will have to work to reduce the temperature. The insulation will slow the influx of heat, but it will not block it. In a rainscreen system, on the other hand, the heat from the cladding will rise up in the drainage and ventilation gap and escape to the exterior. The cladding protects the walls from sun as well as from rain. This saves money by reducing the cooling system’s energy use and allowing for smaller and less expensive cooling equipment.
Rot-resistant materials are a common feature of modern buildings. Durable materials save building owners money because they do not have to be replaced as often, and they are less likely to end up in landfills. Such materials are typically plastic- or cement-based; others may include by-products of industrial processes, such as mining.
One problem with rot-resistant materials is that builders sometimes assume their use allows them to neglect good water management practices. A case in point is the synthetic stucco system known as EIFS (exterior insulation and finish system). In its original incarnation, EIFS was comprised of a hard, polymer-modified coating adhered to a foam plastic insulation layer.
Beginning in the early 1990s, EIFS was the focus of thousands of building failure-related lawsuits. The coating, if cracked or damaged by impact, permitted water ingress. Water that reached the plywood or OSB sheathing was trapped by the impermeable EIFS materials. This led to extensive mold growth and wood decay, which in turn caused indoor air quality problems and rendered the building uninhabitable.
EIFS did not include a drainage and ventilation gap, and most builders at the time were unaware of the product’s flaws. They assumed that EIFS “breathed” like traditional cementitious stucco, which is porous and does not trap moisture. Unfortunately, that was not the case.
Manufacturing rot-resistant products may be harmful to people and the environment. Polyvinyl chloride (PVC) came into widespread use as a building material in the mid-to-late 20th century. PVC was largely deemed harmless until four workers died of angiosarcoma in a PVC production factory in Louisville, Kentucky.
Today, PVC plastic is considered one of the most detrimental in terms of harmful effects. During production, it emits toxic byproducts including dioxin, which has been linked to many cancers, neurological damage, respiratory problems, and birth defects.
Blue Vinyl, a 2002 documentary film directed and produced by Judith Helfand, explored the many negative health effects of its production, use and disposal. The film focused on three communities—two in Louisiana and one in Italy—where PVC is produced.
Helfand interviewed a woman whose husband died because of exposure to harmful chemicals while working in a PVC plant in Lake Charles, Louisiana. In the town of Mossville, pollution from a nearby PVC plant destroyed the groundwater supply. Today, the town is largely deserted. She also interviewed a former plant worker in Italy who survived larynx cancer but at the cost of his voice box.
Some high-performance building solutions are surprisingly low-tech and have been employed for thousands of years.
Porches are a deceptively simple yet ingenious feature of many houses, especially when located on the south façade. In the summer, when the sun is high, the roof of a deep porch keeps the south wall in shade. That reduces the need for air conditioning.
During the winter months, when the sun is low, the porch allows sunlight to warm the south façade. High-quality windows allow the sun’s energy to penetrate the building interior while also retaining it, which reduces heating demand.
Trees can provide similar benefits. Trees and shrubs can block a significant amount of the sun’s energy on a hot summer afternoon, when the sun is lower but intense. In the winter, when the leaves have fallen to the ground, the sun’s warmth can flood in.
Having fewer windows on the north façade can reduce heat loss in winter. Since the north façade receives no direct sunlight, there is little natural light benefit to having windows there. There is an energy penalty for north-facing windows, however, because even the best windows are relatively poor insulators.
One of the most popular ways to harness nature’s power is with photovoltaic (PV) panel systems.
When the sun shines onto a solar panel, energy from the sunlight is absorbed by the PV cells in the panel. This energy creates electrical charges that move in response to an internal electrical field in the cell, causing electricity to flow.
Installing PV panels enables building owners to generate their own clean energy on site, saving money and reducing greenhouse gas emissions.
The federal government has created a tax credit program to incentive Americans to install PV panels on their buildings. The federal residential solar energy credit is a tax credit that can be claimed on federal income taxes for a percentage of the cost of a solar PV system paid for by the taxpayer.
Solar PV systems installed in 2020 and 2021 are eligible for a 26% tax credit. In August 2022, Congress passed an extension of the ITC, raising it to 30% for the installation of which was between 2022-2032. (Systems installed on or before December 31, 2019 were also eligible for a 30% tax credit.) It will decrease to 26% for systems installed in 2033 and to 22% for systems installed in 2034. The tax credit expires starting in 2035 unless Congress renews it. There is no maximum amount that can be claimed. Find out more here.
New Jersey is a leader in promoting renewable energy. The state aims to have at least 4.1% of its electricity sales come from solar power by 2028, and half of its electricity generated from renewable resources by 2030.
To achieve these goals, New Jersey offers various financial incentives, including tax benefits and rebates. These incentives make the switch to solar not only environmentally friendly but also economically appealing to New Jersey residents.
300 Witherspoon Street, Suite 201, Princeton, New Jersey 08542
609.737.6444
© Douglas R. Schotland Architect, LLC 2025